Threaded bushings are supplied by a vibratory feeder bowl with an interior spiral track. Photo courtesy Afag Automation
When screws or bolts are threaded directly into plastic components, failures can occur due to stripped threads or plastic creep. Metal threaded inserts provide serviceable threads for situations when joint strength and the ability to assemble and disassemble the parts without degrading them are required. Polyethylene Foam Laser Cutting
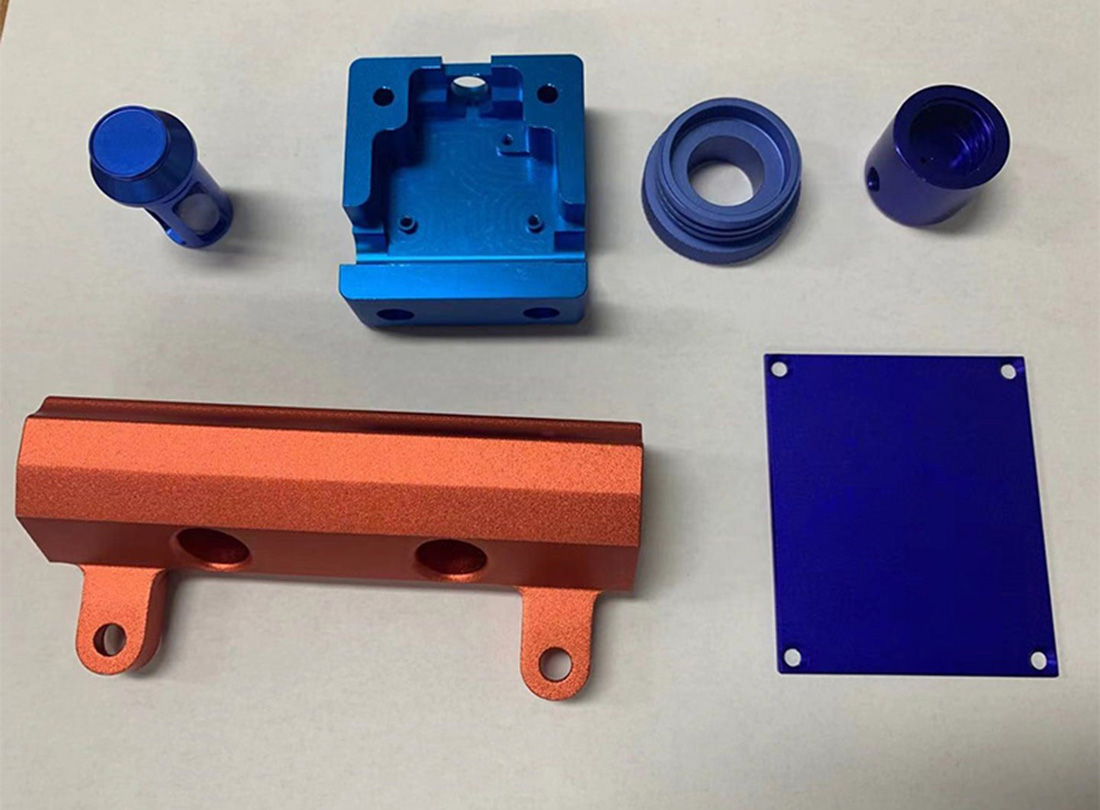
Threaded inserts can be installed during the molding process or afterwards. In the latter case, inserts can be screwed in or pressed in, with or without the addition of heat or ultrasonic energy. Installation of inserts after molding shortens molding time. Post-mold installation also reduces the chance of scrap and mold damage resulting from dislodged inserts.
On the other hand, installing inserts during the molding process saves an assembly step. And, not all plastics are amenable to remelting.
This was the dilemma faced recently by a European manufacturer of battery supports for passenger cars. Ultimately, the company opted for molding-in the inserts. But, that left it with another decision to make: how best to place the inserts into the molds accurately and efficiently prior to injection of the molten plastic.
Initially, the inserts were placed into the molds manually. But, manual insertion could not meet the cycle time requirements, and there was always a chance that a worker could accidently forget an insert. The process had to be automated.
Afag Automation designed and built a handling system that automatically loads inserts into an injection molding machine. The system was installed upstream from the molding machine. Afag supplied every component of the system, including the feeder bowls, grippers and linear actuators. As a result, the manufacturer was able to start using the injection molding machine immediately after installation and integration of the system.
This gantry system automatically supplies insert parts for an injection molding machine. Photo courtesy Afag Automation
The battery supports are produced in both left- and right-facing variants. The Afag system loads four components into the molds. Two of the components—threaded bushings and bolts—are supplied by classic vibratory feeder bowls with interior spiral tracks. The other two components are support plates, which are fed by vertical magazines that are similar to the playing card shoes used by blackjack dealers. Each magazine can hold 120 plates. One supplies the left plates; the other feeds the right ones.
An Afag CS pneumatic linear actuator equipped with a carrier is used to slide a plate out from the magazine and position it for pick up by a gripper. Available in both pneumatic and electric versions, CS actuators come in a variety of sizes and stroke lengths. The compact, rigid slides are designed for millions of cycles.
To load the parts, Afag engineers designed an electric Cartesian motion system equipped with three grippers—one for the bolt, one for the bushing, and one for the plates. A vacuum gripper picks up the bolts. An additional vacuum gripper removes the support plates from the right-hand and left-hand magazines. And, a pneumatic parallel-jaw gripper collects the threaded inserts. Installing three grippers on one linear axis guarantees a smooth, collision-free parts handling process.
The handling unit reliably and accurately positions all the parts, one after the other, on the right-hand or left-hand plates. Every 56 seconds, both cavities of the injection molding machine are equipped with a threaded bushing, four threaded bolts and a support plates for left and right variants.
A vacuum gripper picks up the bolts. Photo courtesy Afag Automation
Due to the tight spatial conditions at the injection molding machine, the loading axis had to cover a relatively long distance. Afag solved this issue with the pneumatic PMP02 gantry module, featuring a stroke length of 3 meters. The actuator features a rigid construction and self-supporting profile. Engineers can set intermediate stops for any number of positions. Repeat accuracy is ±0.1 millimeter, and the module’s maximum payload is 15 kilograms.
Another unique feature of this handling system is that it requires no additional preparation work if the supports are changed. This is because the support plates are fed via two specially designed magazines that can be adjusted to a variety of different geometries.
With a new automated handling system, an auto parts manufacturer has seen a significant increase in efficiency and productivity. Photo courtesy Afag Automation
The engineers designed the supplying system according to the customer’s specifications and subjected it to rigorous testing at Afag’s premises in Hardt, Germany.
With the new automated handling system, the manufacturer has seen a significant increase in efficiency and productivity. The aim is to manufacture 300,000 battery supports every year.
Following final acceptance, the operating and maintenance personnel were provided with training, and Afag will continue to support the system should problems arise.
A manufacturer of premium automation components and a specialist in automated handling systems, Afag supplies linear and rotary actuators, gripper units, feeding systems, pick-and-place units, and turnkey automation systems. The company’s components are guaranteed for 40 million cycles.
For more information on automation components, click www.afag.com. To see a video of the system in action, click here.
For more information on automation components, read these articles: Bowls Supply Parts for Catheter Bowl Feeds Parts for COVID-19 Test Kits Options for Pick and Place
You must have JavaScript enabled to enjoy a limited number of articles over the next 30 days.
On Demand Connecting shop floor tools to a manufacturing execution system is critical to error-proofing assembly processes, improving quality control, and lowering defect and scrap rates. Join Torrence Williams, Partnerships Manager for Pico MES, and Dan Smith, VP of Sales for Kolver Tools, as they discuss an easier path for manufacturers to start connecting their factory floor.
On Demand This topic is something that challenges each of us every day that we go to work. This talk is about change and why it works and why it fails. It is focused on manufacturing facilities, because that is where the author has spent most of his working life.
Copyright ©2023. All Rights Reserved BNP Media.
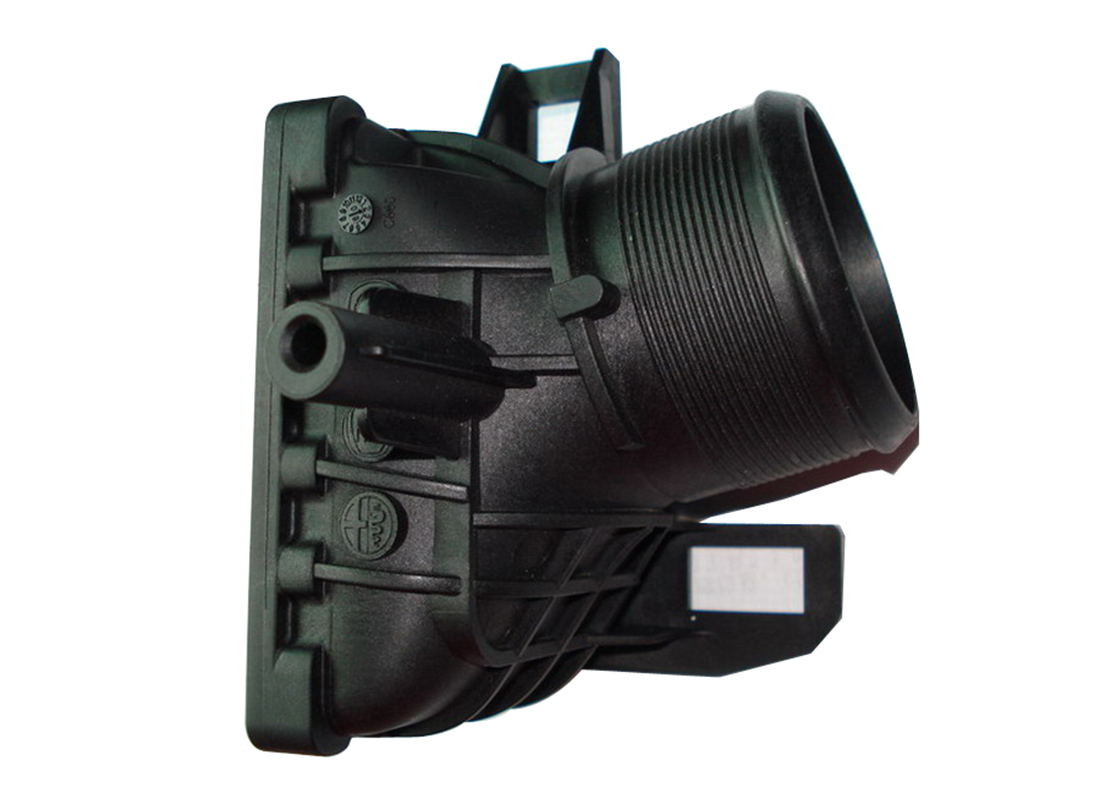
Professional Rapid Prototyping Design, CMS, Hosting & Web Development :: ePublishing