Labor is hard to find, e-commerce continues to grow and evolve, and warehouse capacity is tighter than ever. These challenges have created a warehouse that must have the flexibility to adapt to marketplace pressures with lean staffing.
Here’s where equipment on wheels comes into play. Tuggers, carts and casters are among the most accessible materials handling equipment that can have a big impact on operational efficiency, making the work easier and safer for employees. This equipment segment has also emerged as a compliment to warehouse automation, working in tandem or as part of automated solutions. ED series Medium Duty Caster(60-100kg)
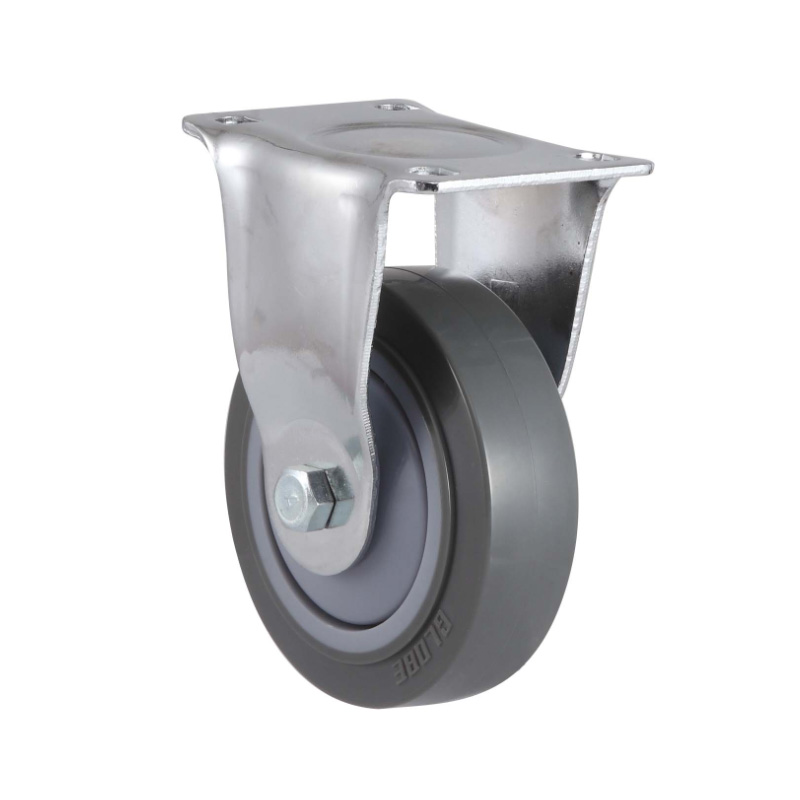
“Robots, palletizers, tuggers, conveyors, mobile carts are all tools that can be used in harmony within a warehouse space as long as the system design accounts for the different tool functions,” says Kevin Ledversis, vice president of sales for Newcastle Systems. “Work will be manual, hybrid or automated in the future. The latter two will help retain staff in challenging work conditions.”
As warehouses move toward a more hybrid approach, tuggers, carts and the wheels or casters that help them move must become more dynamic.
“There’s always going to be a need to move from point A to point B in warehouses. There’s no other way around it,” says Mark Lippert, president of Hamilton Caster. “Our common theme here is we’re all about moving materials within the warehouse. How we do that comes down to: ‘What are the differentiators?’ There’s typically a lot of different applications driving the design or the selection, so the big takeaways are certainly doing it more efficiently, more safely, and with more reliability to where you don’t have to expend labor to replace them as often.”
As the national labor shortage continues to pressure warehouses, an emphasis on efficiency has intensified. Many are implementing modern or even automated tuggers into their operations to help reduce manual work.
“Prior to having a battery powered tugger, many of our customers moved heavy items by gathering 5 to 15 employees to manually push a load or product. With pedestrian-operated tuggers, they can now perform the task with one or two employees,” says Chase Kvistad, sales engineer at PowerPusher.
Creform Corp. developed its automated tugger, or what they call a pin style automatic guided vehicle (AGV), in direct response to the challenges of the labor shortage.
“It’s forcing a lot of companies to look for automated solutions…there’s still so many manpower shortages out there that it’s hard to increase your productivity without some kind of automation now,” says B.G. Edwards, vice president of sales and marketing at Creform.
Creform’s automated tugger is low profile and has a towing pin that can retract to improve manpower requirements for moving carts. The AGV goes underneath a cart, the pin goes up, and it will take that cart to its required destination.
For example, if you bring materials from picking to the order management area, the tugger can automatically deliver these carts, creating a work loop of bringing a full cart in and taking an empty cart back.
“If you have manpower shortages, you want to automate what you can and keep your manpower on your value-added business,” says Edwards.
For those not ready for the large capital investment into fully automated manufacturing, Kvistad is seeing equipment adapted to work with existing carts and systems.
“Customers are using our tuggers to bring carts carrying input materials to feed systems, to shuttle away scrap bins, and move finished product off production lines. We also work with customers who utilize interchangeable tooling that is very heavy. They use our equipment to transport tooling during changeovers before running a different product. Numerous customers, particularly in the heavy equipment and manufactured home industries, utilize conveyance systems to move product down an assembly line. Occasionally those systems malfunction, and they can’t stop production for a day or longer during repairs. Our tuggers are on stand-by to step in and do the heavy moving while maintenance can get the primary system back up and running.” -Kvistad
A hybrid approach is another option for warehouses that have not been fully automated.
“We’re seeing more people utilize a combination of carts and tuggers as a flexible solution that’s much less expensive than doing like autonomous mobile robots or large transfer carts that are individually powered,” says Lippert. “If you have multiple things to move around that are fairly heavy, you can design low-cost carts, and then you only commit or invest in one specific tugger that can pull or push multiple carts or equipment throughout the shop. That’s actually a more economical way for automation than, let’s say, independent powered transfer carts.”
Tuggers also play an important role in managing forklift operations, with warehouse operators looking to reduce and re-allocate forklift traffic or eliminate the misuse of forklifts in specialized applications. Tuggers are ideal for moving smaller loads or in tight spaces where forklifts can’t fit.
“Forklifts are great for lifting heavy materials and transporting short distances, but they’re bulky, expensive and require a lot of training to operate,” says Kvistad, noting that tuggers in comparison are more compact, ergonomic, emission free and require minimal training.
Casters are all about mobility, moving material safely, efficiently and quietly within the warehouse. They can have a huge impact on how well your equipment works and how easy it is to use—two major keys to retaining warehouse workers.
“Casters can obviously improve the production flow dramatically—and add a lot more flexibility,” says Hamilton’s Lippert.
This flexibility is more important than ever as companies look to automation to fill the labor gap. Hamilton Casters, specifically, continues to broaden its product line to work with automated equipment and create custom solutions to meet customers changing needs.
“A few years ago, we introduced a line of continuous-duty casters designed for AGVs and AMRs. We’re also promoting our custom engineered product line, and we’re seeing quite a bit more demand for custom engineered stuff. That’s an indication of the increase in demand for automation, where with automation, automated machinery and equipment standard items won’t work, and they need to customize.” - Lippert
Finding the right casters or wheels for your equipment ensures it works right, can help lower the noise level in the factory, and reduces operator fatigue. To get the most out of your equipment, it’s important to consider how your operations are unique and choose the best setup to fulfill your needs.
“With the correct configuration, a single employee can safely perform the role of many employees. Operators require minimal training, simultaneously increasing safety and efficiency,” says Kvistad.
He adds that because each customer has unique requirements when it comes to operating environment, safety standards and production demands, custom solutions have grown in popularity over the last few years.
“Our ability to engineer and fabricate custom attachments enables our equipment to fit within any application,” says Kvistad. “Safety and ergonomics are always at top of mind when our customers list their needs. For that reason, all our equipment now features an ergonomic handset with hand guards, variable speed rotary throttle with neutral braking, horn and belly safety switches. We also offer strobes, beepers, custom wheel guards, proximity sensors, laser curtains and more.”
Carts are an easy and affordable way to standardize work in the warehouse. They can be modified based on width or height to meet your specific needs, and some are even getting smarter. Carts offer a convenient and efficient way to transport heavy loads, playing a huge role in the overall safety of your warehouse.
Most carts in the warehouse are used for materials handling, but they can also help be effective tools for improving operator efficiency. Mobile workstations, for example, reduce wasted motion acting as a desk on wheels, which can improve metrics, accuracy and speed. Workers can go where the work happens instead of taking things to static stations.
“Someone may have a mobile powered workstation, which becomes their desk essentially—PC, printer, warehouse management system, scanner—and also use a tugger in receiving to move materials,” says Ledversis at Newcastle. “If things are on wheels, you have a more flexible workspace and enabled employees who can go to the where the work needs to take place.”
These workstations have become increasingly integrated and ergonomic, with lighter lithium iron phosphate batteries that run and last longer and are easier to use. Batteries are also now swappable, reducing downtime.
Picking carts are also seeing technological advances, helping to further optimize the job. While most warehouses still use basic, manually operated carts, interest is growing in automated solutions.
Creform offers a picking cart with light automation integrated by a third party. These carts are manually driven down the line, but when it gets to a certain area, it notifies the operator to pick a part there. It also lights up which bin the part goes in and how many.
“Our picking carts are very lightweight, and they’re designed to hold a specific number or jobs or orders per cart,” says Edwards. “The beauty of our picking carts is they’re very easily moved throughout the facility. Operators are not as worn down from pushing heavy carts through the warehousing area.”
And at the heart of all these solutions is creating easier, safer and more reliable solutions.
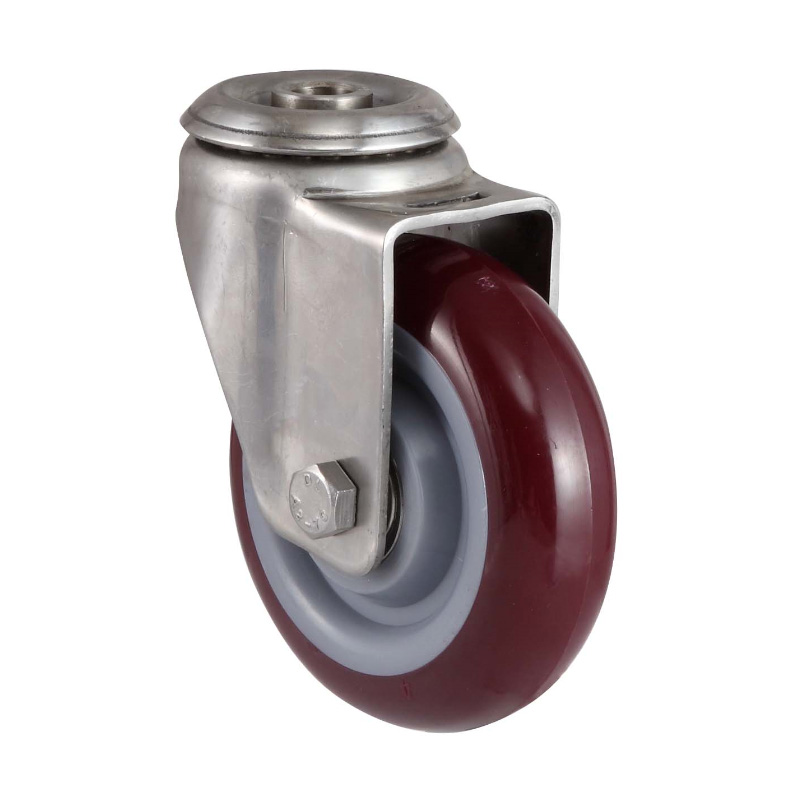
Neoprene Chair Casters “Safety, ergonomics and efficiency are at the forefront of the industry,” says PowerPusher’s Kvistad. “Implementing a well-planned system for moving heavy materials on cart/caster setups, propelled by a pedestrian-operated, battery powered tugger, affords manufacturers the optimal solution for employees working safely and efficiently. A tugger and cart/caster setup allow manufacturers to minimize forklift traffic and risk of injuries while keeping pace with growing production demands.”