As did their predecessors, five-axis machine tools on the market today use the X-, Y- and Z-linear axes, plus two rotary axes so that tools can get to more sides of a part with no extra setup. But the current crop of systems are the beneficiaries of hardware and software progress that significantly improves the experience and results of five-axis machining.
What’s more, five-axis users now have a vast menu of options that allows them to find machines that are well-suited to meet specific requirements—both from a technological and a financial standpoint. die-casting-metal-parts
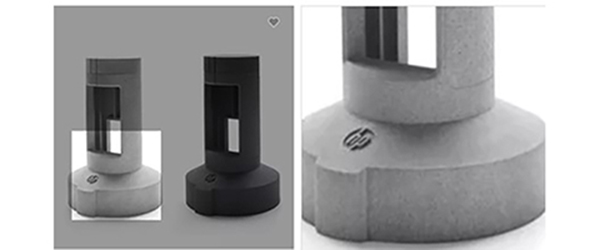
Some important five-axis advances can be attributed to technological progress in general. In the early days of five-axis machining, for example, computer technology had trouble keeping up with the requirements of complicated cutting routines, recalls Jared Leick, machining center product group manager at Mazak Corp. in Florence, Ky. “We would actually be able to starve the machine for knowledge, meaning that the computer could not process code quick enough to run some complex shapes,” Leick says. As a result, machine movements could be herky-jerky rather than smooth, causing abnormal blend lines and other undesirable results.
Thanks to improvements in CNC hardware such as solid-state drives and increased memory, Leick says the latest five-axis machines “are able to crunch code very fast, so the machine is never waiting for information.”
Another recent advancement is the ability to feed machining data directly into a five-axis CNC using a CAM system. This development, which Mazak has been working on with software vendors, cuts a number of steps from the information-transfer process, according to Leick, which can significantly reduce prototyping time. In addition to sending full programs directly from an outside computer to a machine control, he notes that the process can be used to modify existing machining programs on the fly.
If a small change is needed in a program parameter, for example, Leick says, “you could do it real quick on your computer, then send the new code in a matter of seconds instead of the minutes that it would probably have taken to do it the (traditional) way.”
To facilitate rework in some cases, a CNC feature recently added by a number of machine builders allows five-axis machining to commence even if the rotary axes aren’t in the zero-point machine position, according to Errol Burrell, machining center product manager at Okuma America Corp., Charlotte, N.C. So if a part needs rework on a five-axis Okuma machine, it can be done even if the part isn’t positioned in the workholding exactly the way it was the first time it was machined. In situations like this, Burrell explains, the machine can probe the new setup so the necessary adjustments can be made to the rotary axes that allow five-axis movement to start.
A major development impacting five-axis machines is based on the premise that production-related activities that stop actual machining should be eliminated if possible. These include:
To achieve this goal, many shops are turning to software that allows them to accurately simulate the machining process and environment. One example of this type of software is Siemens’ Run MyVirtual Machine (RMVM), which the company describes as the “digital twin” of the actual CNC machine. Available with Siemens’ Sinumerik One CNC, shops can use an RMVM digital twin for offline programming and training, as well as for checking machining programs and processes before cutting begins on the real machine.
RMVM can’t replicate exactly what happens in a machine during the cutting process, but operators get “as true a one-to-one (correlation)” as possible, according to Daniel Vitullo, Midwest territory manager for Siemens Industry Inc. in Elk Grove Village, Illinois.
“There are a lot of different simulation tools out there, and they’re very good products,” Vitullo says. “But (RMVM) is running the simulation using the same control that’s running on the machine. And you’re doing it on your PC, so you’re not actually using the physical machine’s control.”
In addition to the virtual CNC, RMVM is available with an option called /3D that allows it to provide a virtual image of the machine space, tools and clamping devices that will be used in an actual cutting process. The /3D option lets users view the full operation of the CNC and machine for training purposes, and also check the clamping and machining of a particular workpiece from a variety of angles. During machining simulation, all collisions are detected, displayed and logged.
While simulating any machining process beforehand can be useful, it’s particularly helpful and reassuring to see a complex five-axis machining routine run smoothly and collision-free before the actual cutting begins.
Given the expense of a five-axis machine, which can range from $400,000 to $3 million, it’s imperative to keep it running and validate any changes before they’re implemented. “If you’ve got a 50,000- or 200,000-line (software) program that just came down from the mothership and they say, ‘Put it in the machine and run it,’ you would have a lot more confidence when hitting cycle-start if you ran it through this simulation first,” Vitullo says.
In some current offerings, the latest five-axis technology is supplemented by capabilities normally provided by separate machines. To this end, DMG Mori USA in Hoffman Estates, Illinois, is aggressively pushing the idea of packaging a number of different machining technologies in a single system, according to Luke Ivaska, the company’s manager of national engineering and technical sales. An example of this would be combining five-axis milling, turning and grinding in one machining platform.
“What we see a lot of times, especially in aerospace applications, is that a part travels through various different stages and machines,” Ivaska explains. “It may start off in a lathe for a turning operation. Then it sits and waits to go into a mill. It goes through the mill and then it sits and waits to go into a grinding machine. So there’s a substantial amount of work in progress in various stages, and some of that has very long lead times. And if one of those platforms goes down, then that whole train stops.”
By contrast, there’s no waiting time between different machining operations when they’re all combined in one system. As a result, Ivaska says, a multi-step manufacturing process that might take six months when it involves several machines could possibly be completed in six hours by a single multifunction unit. In addition to boosting throughput, a multifunction system takes up much less floor space than several single-function machines.
Moreover, Ivaska adds, replacing multiple machines with a single system reduces setups and machine maintenance. These benefits have become more attractive than ever at a time when shops are having trouble finding people to perform such tasks.
On the downside, Ivaska points out that the upfront cost of a multifunction machine is higher than that of a conventional single-function one such as a five-axis mill. And a system that combines grinding with five-axis milling and turning will probably fall a bit short of the accuracy that a stand-alone grinding machine can deliver.
Shops that don’t have extreme accuracy requirements, however, might be able to get what they need by spending an extra $100,000 on a multifunction machine with grinding capability rather than shelling out up to $1 million for a stand-alone grinder, Ivaska asserts.
Another type of multifunction machine offered by DMG Mori is one that packages automation with five-axis milling and turning. Introduced in 2022, the company’s NTX 500 is a full five-axis, turn-mill machine with an integrated robot for part loading and unloading. Designed for high-speed and micro machining, the NTX 500 has found a home in shops that produce medical and aerospace parts, according to the company.
No matter how attractive the latest options might be, shops won’t purchase a five-axis machine if they can’t fit it into their budget. However, those shying away from the technology for cost reasons could face a stark reality.
Okuma’s Burrell asks, “Can you afford not to have it in this day and age, especially when you see the accuracy that customers are requesting now? I think people are designing parts simply because they think (shops) have this technology now.”
Fortunately, five-axis technology is becoming more affordable. In fact, Okuma has introduced a line of five-axis machines dubbed “Affordable Excellence.” The idea, Burrell explains, is to hold the price of these machines down by limiting the options available to buyers, while providing the same five-axis functionality and quality offered by Okuma machines with heftier price tags. Though Affordable Excellence buyers can’t choose whatever spindle and tool magazine they want, they will get a five-axis machine built exactly like those in more expensive lines, he says, adding that the concept has been very popular with customers.
Other machine-tool builders also are increasing the breadth and diversity of their offerings. “If you look at the spectrum of five-axis machine tools on the market today, there is generally something for everybody and almost every price range,” notes Tom Dolan, vice president of Mitsui Seiki USA Inc., a machine manufacturer in Franklin Lakes, N.J.
Besides fitting into a wide variety of budgets, current five-axis offerings can handle a wide range of applications. At one end of the spectrum, Dolan says, are complex and expensive components such as turbines with many blades that have to be individually machined. These high-end components must be cut from solid blocks of various challenging metals with continuous five-axis motion, possibly at speeds of hundreds of inches per minute. In addition, the machines must be able to maintain high levels of accuracy as they go through demanding cutting routines over and over again.
On the other hand, he points out that five-axis machining centers are also used to manufacture relatively inexpensive automotive parts with less stringent tolerance requirements and made of easy-to-machine materials. These parts need to be produced quickly, but, as with more expensive components made with five-axis technology, they require machining on multiple faces.
Dolan also notes that the latest five-axis offerings come in many different sizes to accommodate widely varying part dimensions. Some shops, for example, need big five-axis machines to manufacture large aluminum airplane parts that must be sculpted into complex shapes at high speeds. Others require smaller five-axis systems for the micro machining of tiny components for everything from medical devices to space satellites. One example of the latter is Mitsui Seiki’s PJ 303X five-axis machining center, which the company showcased at IMTS 2022 in Chicago.
“You needed a magnifying glass to see the workpiece” machined by the PJ 303X, Dolan boasts. “And we were holding a tolerance of less than 0.5 µm in full five-axis contouring of these tiny parts.”
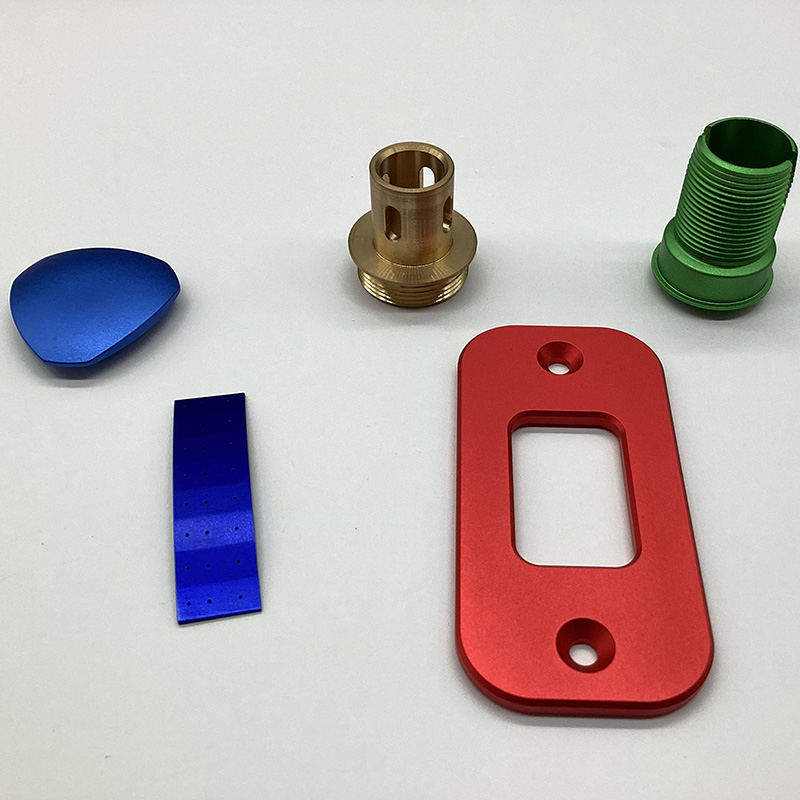
Prototype Machining The variety of five-axis options on the market today has even put complex machining within the reach of new entrants into the manufacturing field.